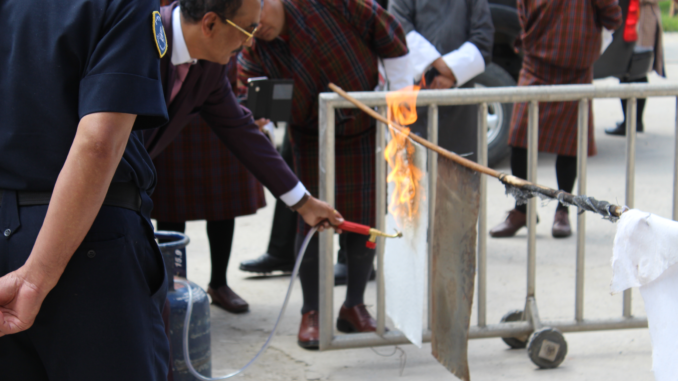
Fire is activated only if Heat, Fuel and Oxygen are present together at a time. These three elements are called fire triangle. Even if there is no any ignition spark, fire gets activated when all three are present and heat is beyond combustion temperature of fuel.
The average loss due to structure fires alone is $22,244 per year. Wildfires result in $10 billion in direct property loss. Public assembly fires include fires in eating and drinking places and other entertainment venues, houses of worship and other places where people congregate. These fires caused roughly 3,700 civilian deaths, 16,600 civilian injuries and $14.8 billion in property damage in 2018 in US alone.
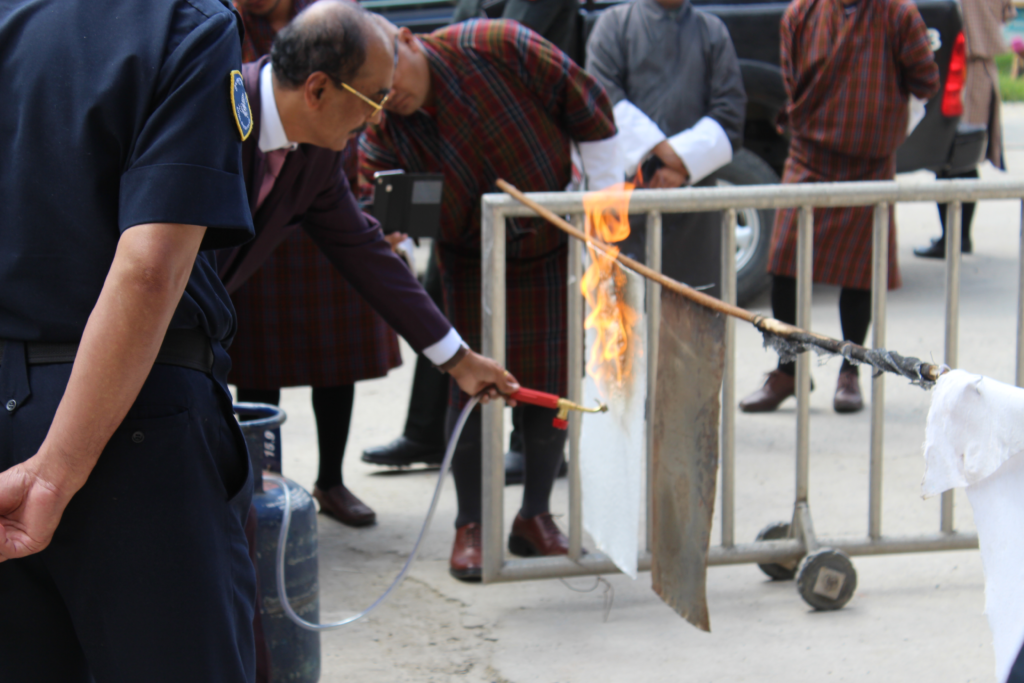
To prevent these fire incidents, buildings are two types of protections. One is active fire protection and passive fire protection. In basic terms, Active fire protection is about detecting, stopping and escaping fire. Whereas passive fire protection means containing the fire and preventing it from spreading further. You need both an active and passive fire safety system working together to prevent, detect and alert, restrict and potentially suppress a developing fire.
Fire prevention coatings fall in Passive fire protection system due it’s nature of containing, preventing it from spreading and suppressing fire. These fire prevention coatings are mainly of three types.

Fire resistant coatings
Fire resistant coatings are coatings which contain chemicals which do not allow the coating to burn. They become black at area directly in contact with fire but do not allow the fire to spread than the area directly in contact. This is useful for spread of flame to other areas. These are called Non-Intumescent coatings. These coatings are good for resisting fire at initial stage. These are generally used for curtains, papers, thatched roofs, less fire prone areas. They are rated as class A, B and C depending on their spread of flame resistance. In non-intumescent fire retardant coatings, the fire retardant additives are mainly flame retardants. Commonly used organic compounds containing phosphorus and halogen as well as antimony, boron, aluminum series and magnesium series compounds. UGAM Non Intumescent Fire Retardant Coatings is classic range being manufactured for these types of fire resistant coatings.

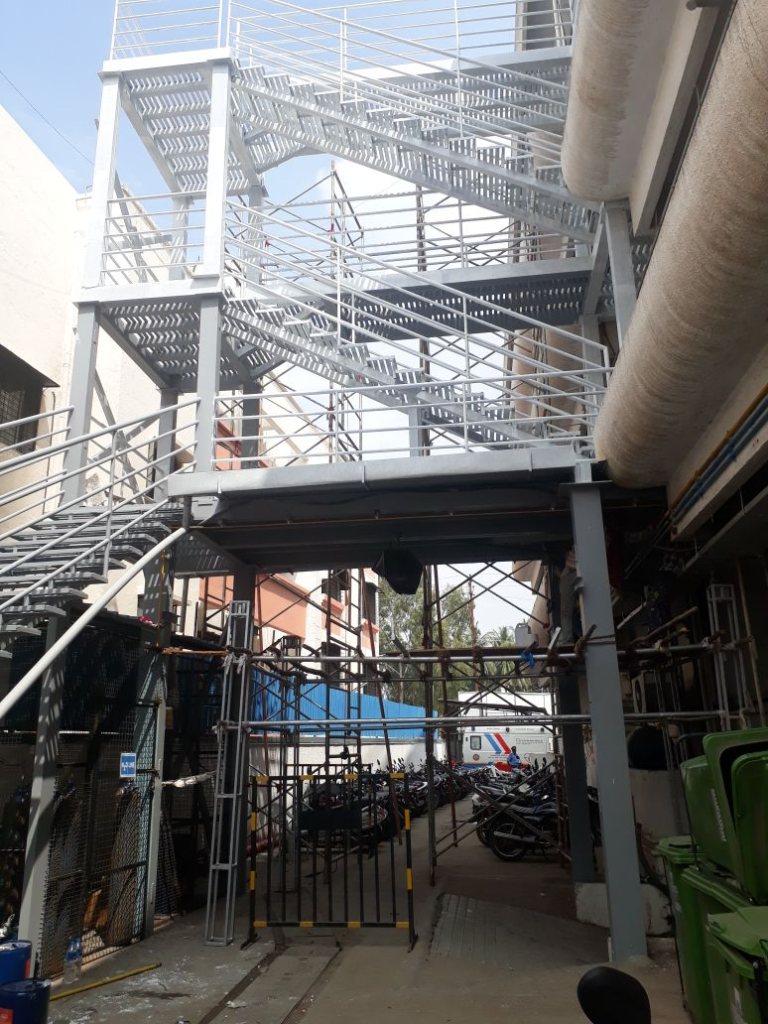

Fire retardant coatings
These coatings when in contact with fire and above 250 deg C, react and form charred foam generally 20 times the thickness of the coating. This foam is fire resistant and having property of thermal insulation. Because of this, the foam does not allow the temperature to reach to the base surface. If the base surface is wood or flammable, it does not get Oxygen and Heat; hence it does not burn or spread the flame. If the base surface is structural steel, it does not get heat and hence structural stability of the steel is maintained. Steel looses its structural stability beyond 535 deg C. These coatings are called Intumescent coatings because of its reaction and forming foam at elevated temperature to block Oxygen and Heat. These coatings are coated to required thickness as per fire rating required. In general fire ratings are 60, 90 and 120 minutes. Fire rating is the time for which the coating will prevent spread of flame or temperature conduction to bare surface. During this time the fire fighting team can arrive and the person and important property can be evacuated. There are mainly three major components in the intumescent fire-retardant coating composition: (1) acid source, (2) charring agent, and (3) foaming agent. While burning, intumescent components form a protective char with releasing of volatile gases such as ammonia and nitrogen. These coatings have low smoke and low toxicity. UGAMCOAT 06022007, UGAMCOAT07022007, UGAMCOAT290908, UGAMCOAT141098 are intumescent type fire retardant coatings for wood, walls, cables and structural steel respectively.
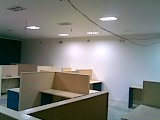
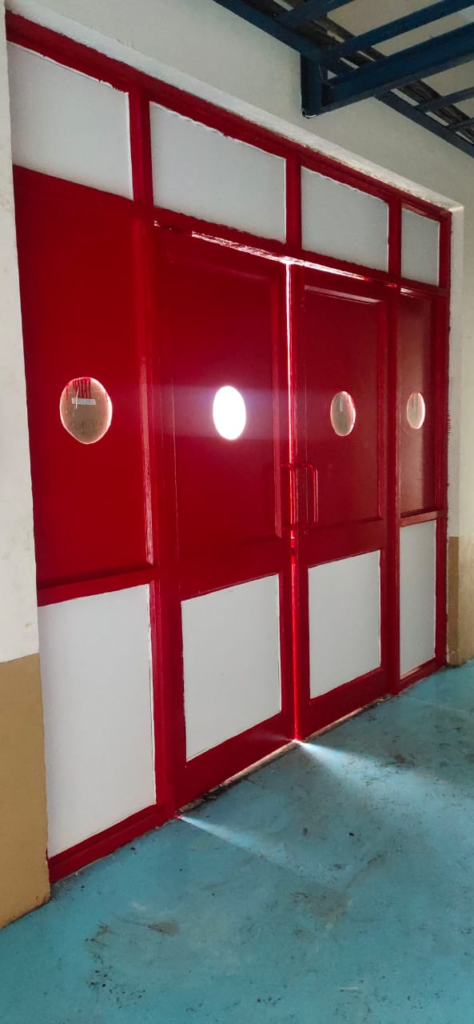

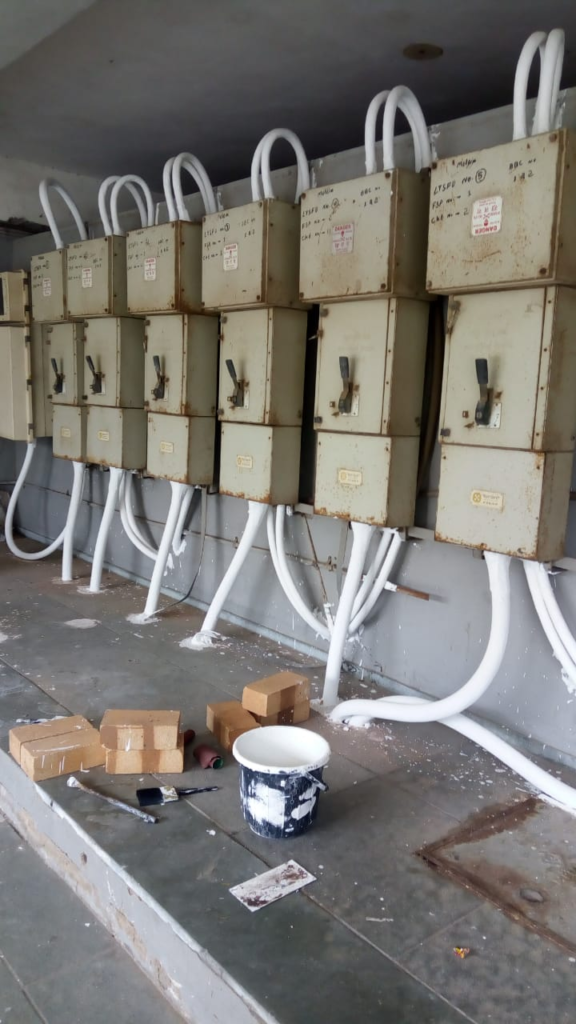
Fire proof coatings
These coatings are not affected by fire and have thermal insulation properties in them. These are generally used on structural steel. But the problem with these coatings is they require very high thickness around 25mm and increases weight on structural steel thereby increasing the cost on structure. These are mainly cementitious or gypsum based coatings and having exfoliated vermiculite, perlite or other thermal insulation materials. They also contain ceramic fibers for bonding and withholding high thickness. Above 25 mm thickness generally wire mesh is incorporated to take care of expansion cracks in those coatings. Because of all these, the application of these coatings becomes tedious process and hence intumescent coatings are preferred over these coatings. UGAM Vermiculite F R Coating is widely used coating for structural steel coating for fire proofing. This coating can achieve four hours fire rating. The thickness of these coatings is derived from Hp/A which is surface area/ cross sectional area of each member used in construction. Also the time rating required and temperature are the factors which define rating of these coatings.
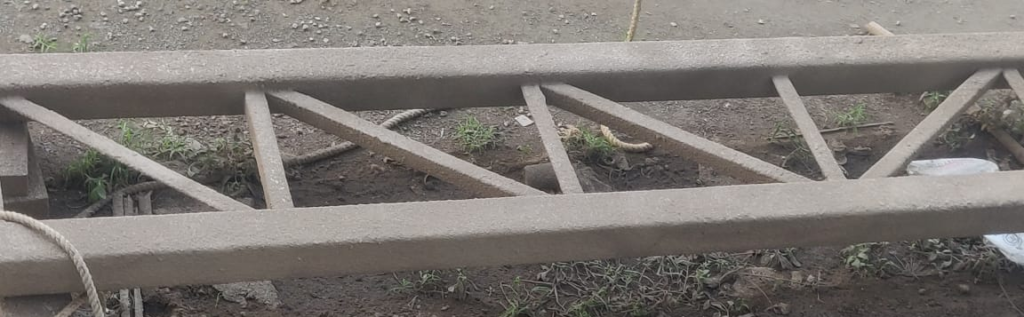
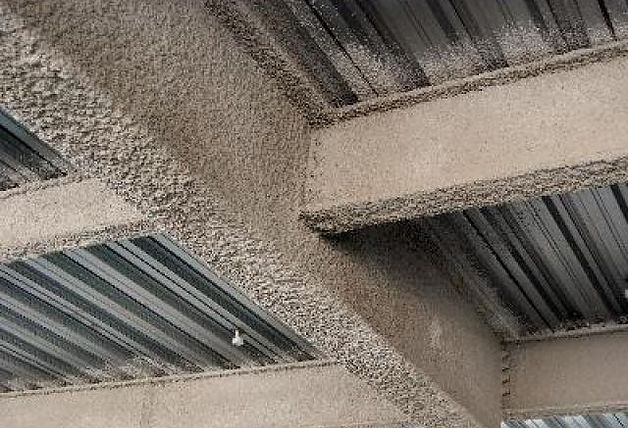
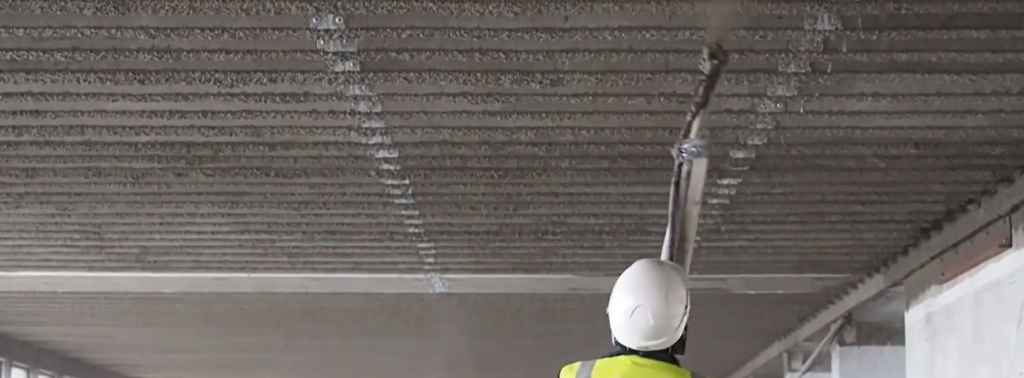
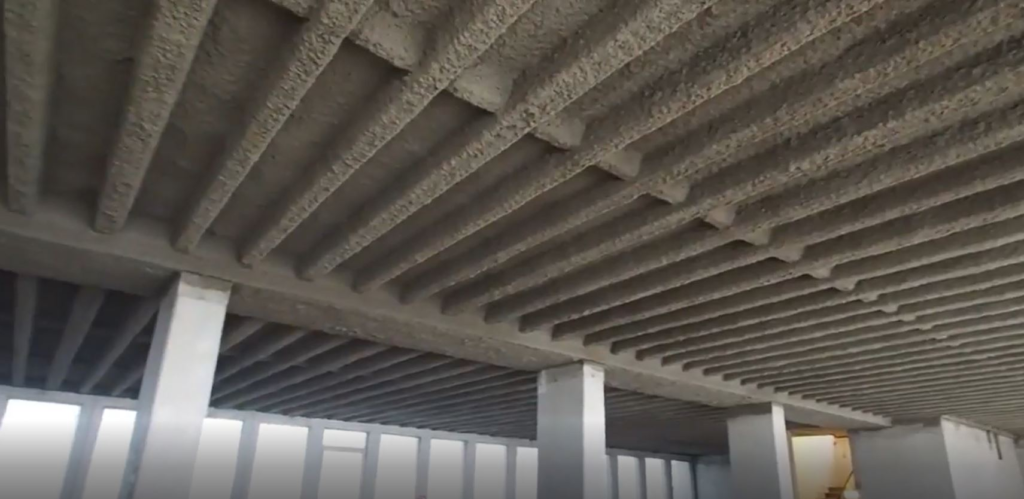
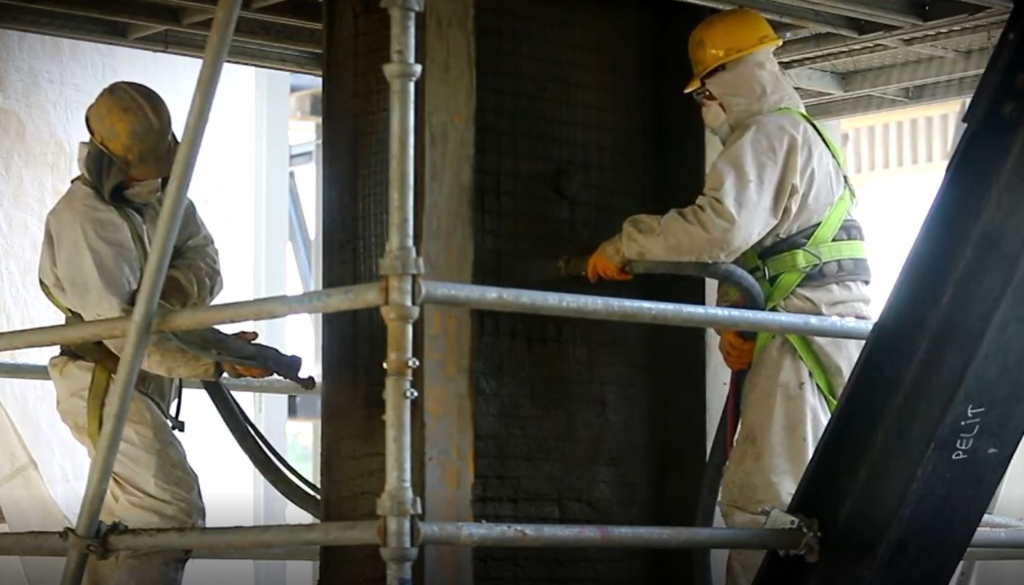
Be the first to comment